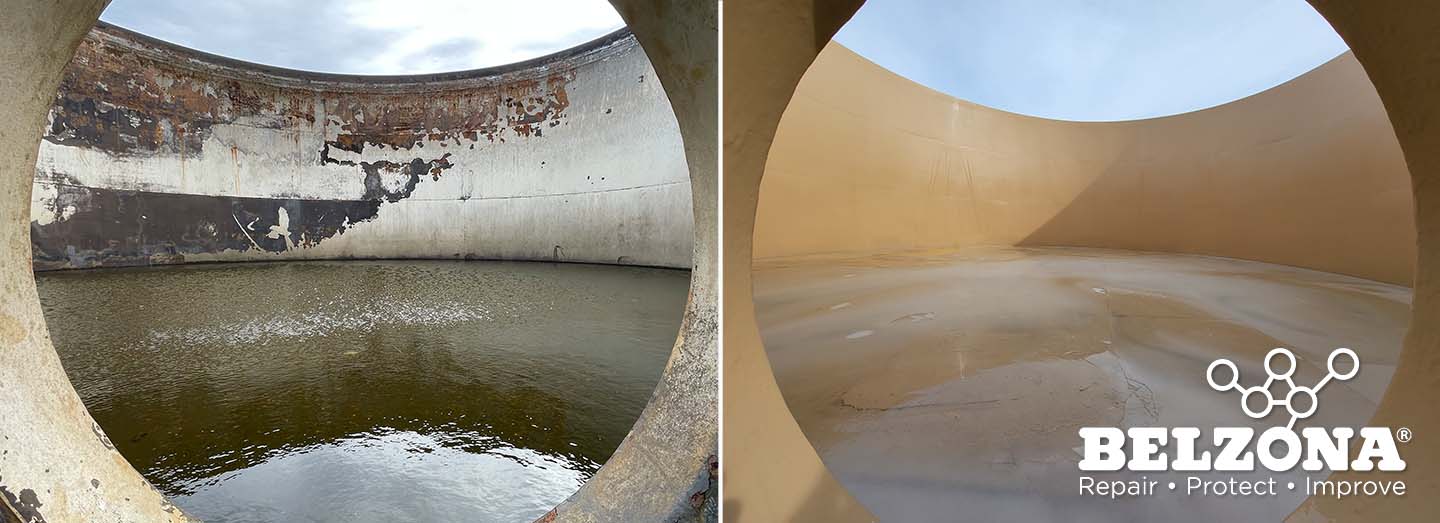
Internal Tank Coating and Vessel Linings Services
Banks Industrial Group (BIG) provides tank coating and vessel linings services to shield valuable assets against chemical exposure, abrasive solids, continuous immersion, elevated temperature, and high-pressure operating environments. With our protective coatings, we prevent metal loss and reduce the risk of forced shutdowns and unplanned downtime. At the same time, our epoxy linings cure rapidly and are applied directly to the surfaces for rapid return to service.
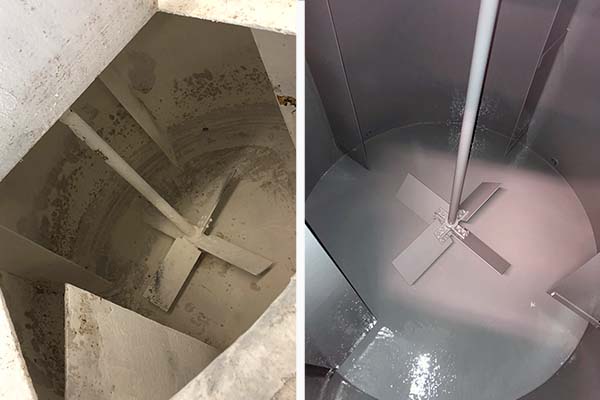
Water treatment lime tank protected with chemical and abrasion resistant epoxy lining.
Request Estimate
BIG Internal Tank Coating and Vessel Linings Services Benefits | |
Reduced Downtime | We reduce downtime with rapid application and fast-curing capabilities. |
Extended Asset Service Life | We extend asset service life by protecting against tank and process vessel corrosion, erosion, and abrasion. |
Chemical Resistance | BIG’s internal tank coating and vessel linings offer excellent chemical resistance against a wide range of acids, alkalis, and hydrocarbons. |
Durable Barrier | Our coatings and liners provide durable barriers for tanks and process vessels operating under continuous immersion, including those at elevated temperatures. |
Easy Application | BIG applies coatings using a brush or spray for large surface areas with rapid curing at room temperature—no hot work needed. |
Reduced Health and Safety Risks | Our VOC- and solvent-free materials lower health and safety risks in confined spaces. |
Fit for Purpose | We use industry-leading Belzona epoxy coatings backed by comprehensive testing and extensive historical data, enabling us to provide a fit-for-purpose solution for your operating environment. |
Start-to-Finish Services | Our services include site evaluation, surface prep, competent person application, and ongoing testing to verify the condition of internal linings. We also repair holes, cracked weld seams, and severe metal loss. |
Applications of Our Internal Tank Coating and Vessel Linings
BIG’s internal tank coating and vessel linings services have applications in a range of industries, including:
-
Food & Beverage: tanks and silos requiring hygienic environment for drinking water and food contact
-
Pharmaceuticals: settlement tanks, mixing tanks
-
Facilities: hot water tanks, fire water tanks, and thermal energy storage tanks
-
Oil, Gas & Chemical: storage tanks and process vessels operating at high temperatures and pressures and/or handling amines, liquid hydrocarbons, gas, and process chemicals
-
Water / Wastewater: mixers, clarifiers, settlement tanks, aeration channels, and buffer tanks
-
Patch repair for existing coatings such as glass flake and ebonite
Tank Corrosion Problem/Solution Example
Problem: Possibility of forced shutdown due to tank minimum wall thickness from corrosion
Corrosion prevention methods such as protective linings, passivation, cathodic coatings and claddings will deteriorate over time. Chemical exposure, abrasion, immersion, elevated temperature, high pressure, or a combination of these factors will eventually break through to the carbon steel substrate. The result is corrosion and metal loss damage to your asset.
The deterioration will eventually force a shutdown due to potential leaks and loss of containment. Unfortunately, internal lining repair or replacement is challenging considering the high cost of downtime, lost production, and restarting. Potential safety issues and environmental contamination further complicate this situation.
Solution: Rapid rebuild of metal loss and application of tank lining to shorten downtime and extend service life
Applying an appropriate epoxy tank lining is an effective option to minimize downtime and give your assets lasting protection. Applications are done in place and typically cure within 24 to 48 hours. This is much faster than rebuilding process vessels or components using metal clads or increased metallurgy, which can take weeks or months. The time saving gained from using epoxy tank lining often results in significant cost savings during an unplanned stoppage.
There are two essential factors needed to make an epoxy lining work:
-
Selection of a coating that is fit for purpose
-
Competent prep and application
Coatings must be suitable for the intended operating conditions and applied correctly with best practices. Anything less will lead to premature lining failure. However, when properly selected and applied, epoxy tank linings are robust — even in process vessels where elevated temperature, high pressure, steam-out cleaning, and explosive decompression are brutal.
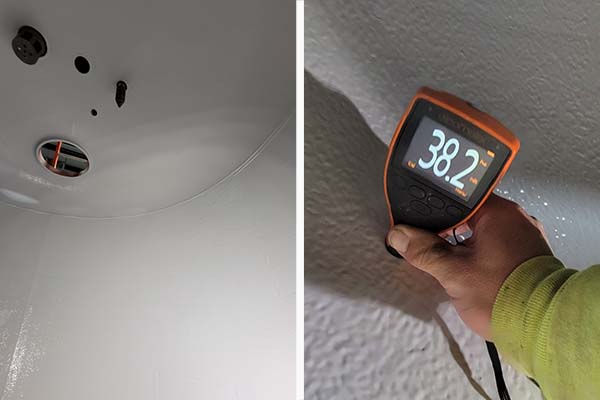
Testing of internal tank lining and wall thickness helps predict problems and avoid forced shutdown.
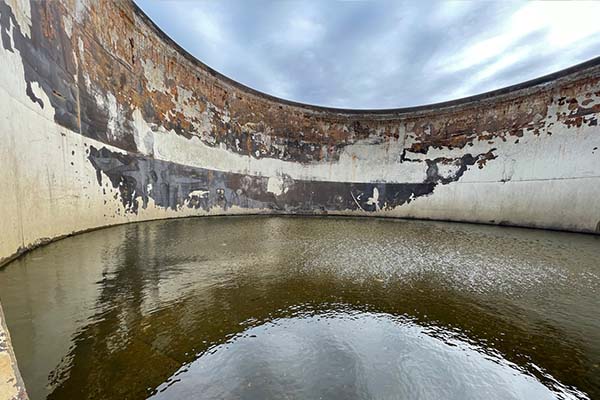
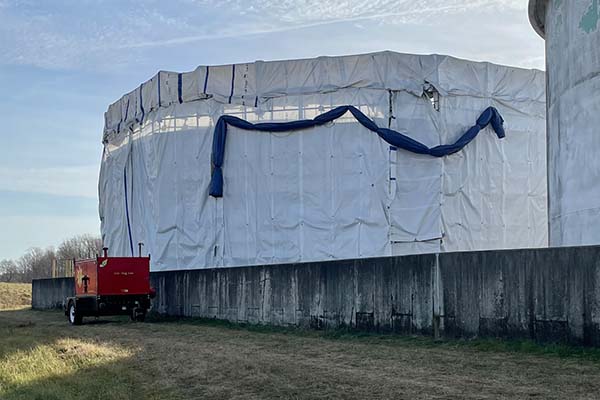
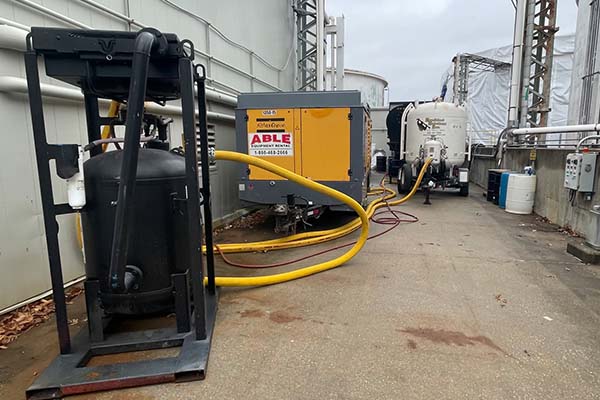
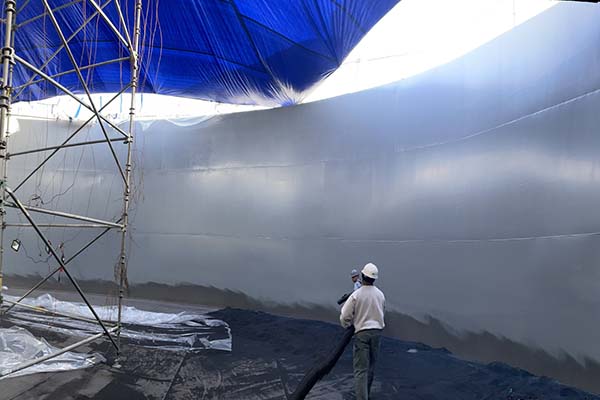
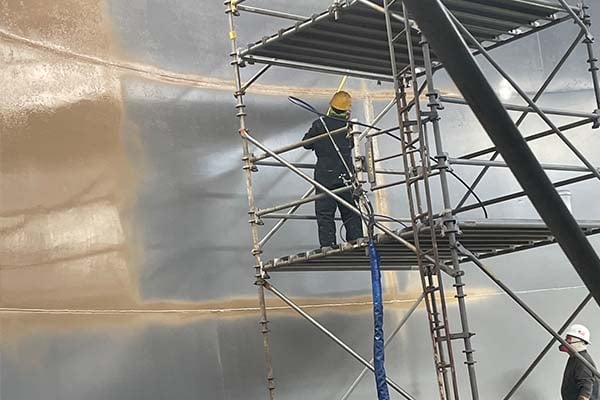
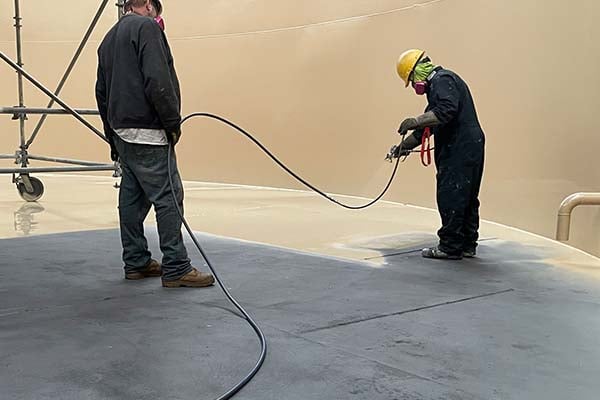
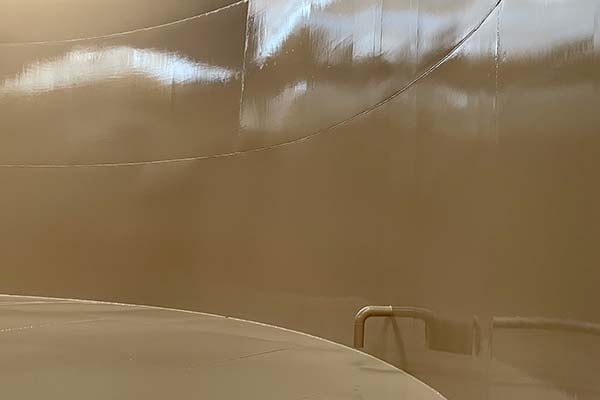
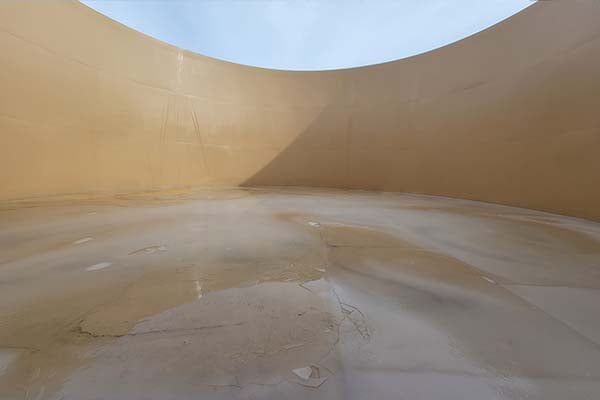
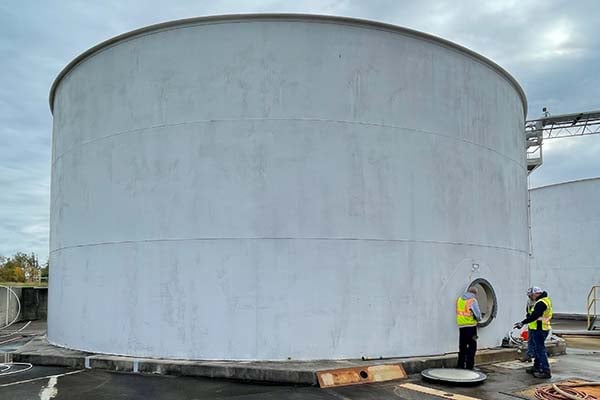
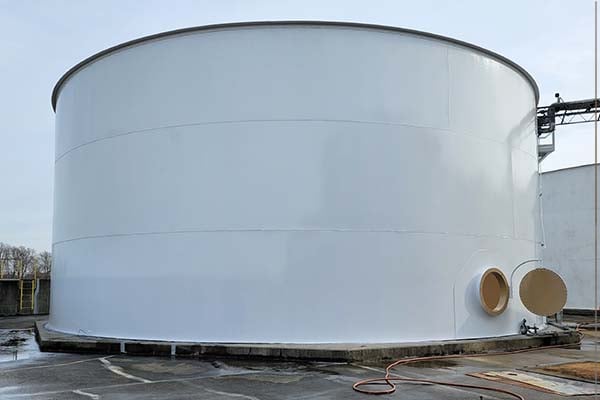
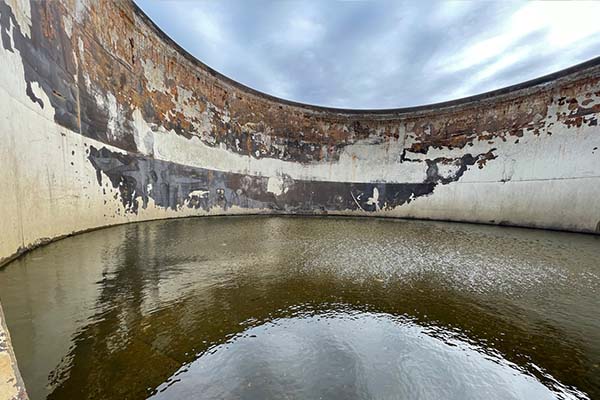
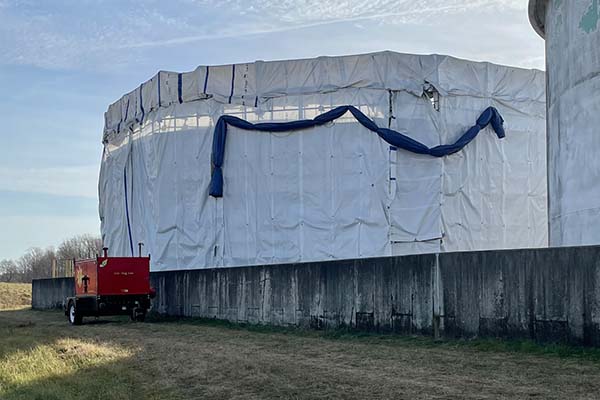
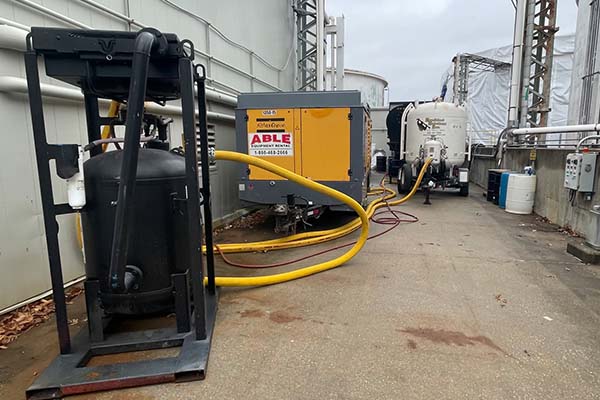
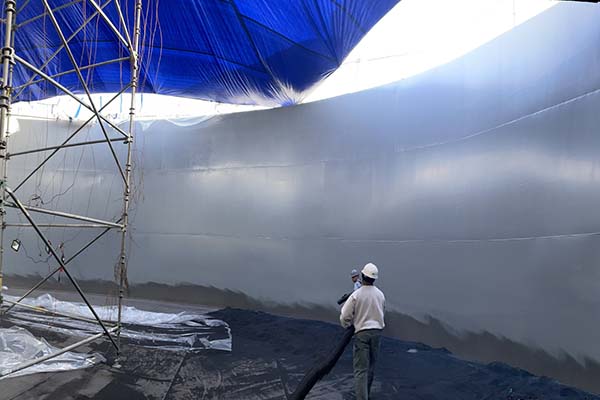
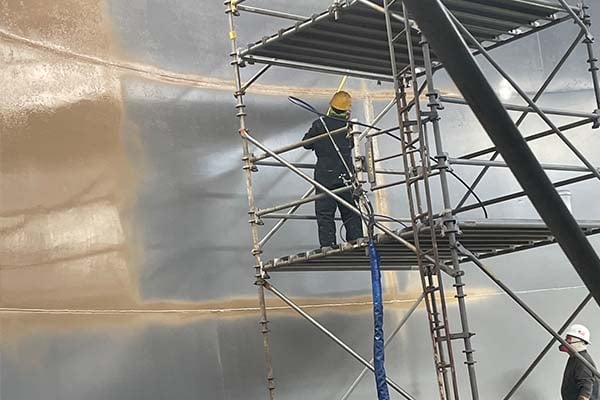
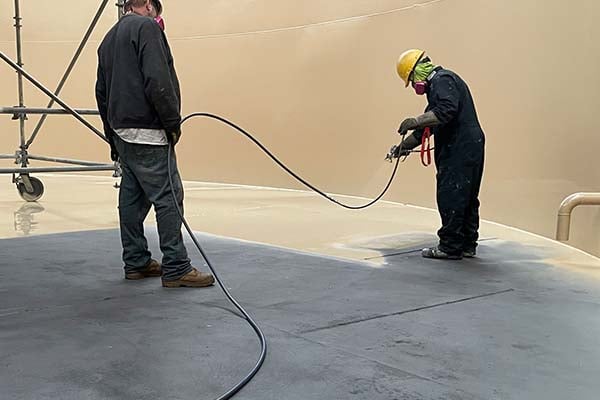
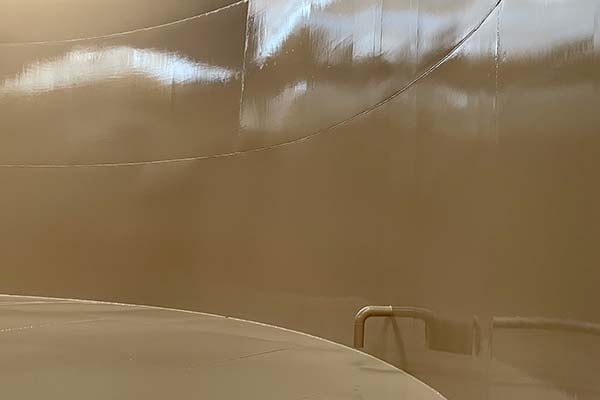
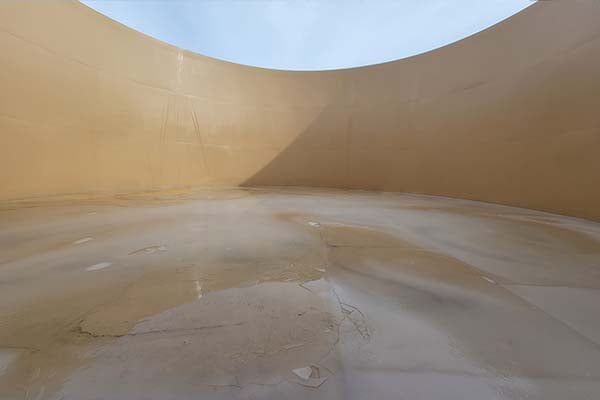
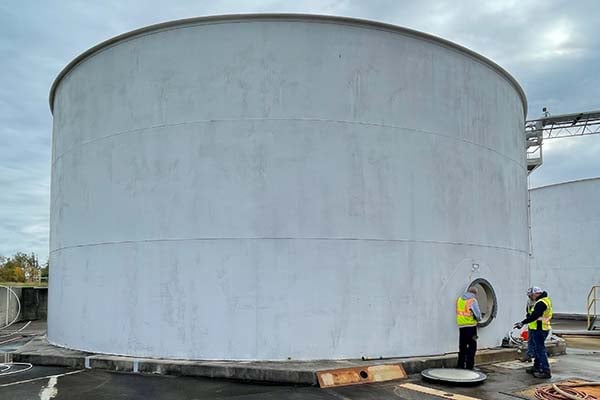
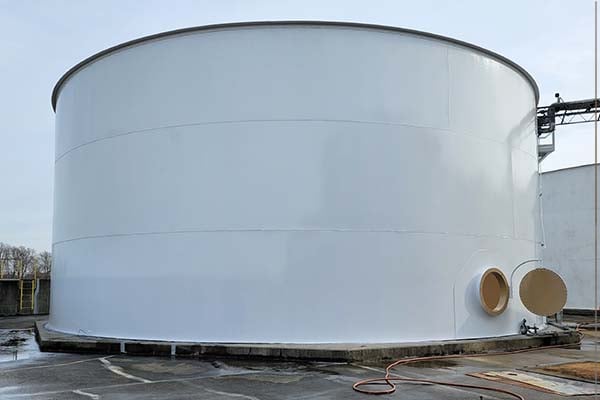
Tank Lining Example
The tank shown above is part of a water remediation system at a superfund cleanup site in NJ. Interior corrosion was blasted to white metal in a climate-controlled enclosure, then lined with a chemical resistant epoxy coating suitable for continuous immersion. The tank exterior also received a barrier coating to protect against weather and UV wear.
How Can Banks Industrial Group Help You?
BIG provides turnkey industrial tank and process vessel internal lining service. We understand the high cost of shutdown and restart and work diligently to apply an effective, long-lasting protective lining with a fast return to service.
The Belzona epoxy tank coatings and linings we use have been extensively tested and proven effective in the field. As a result, we can provide you with a solution that meets your exact requirements and provides long-term protection.
We handle all phases of application, including blasting, rebuilding, and coating. Following completion of the work, we measure the wall thickness for ongoing testing. This allows future verification of coating performance in an otherwise hidden area and estimation of coating service life and maintenance to avoid forced shutdowns.
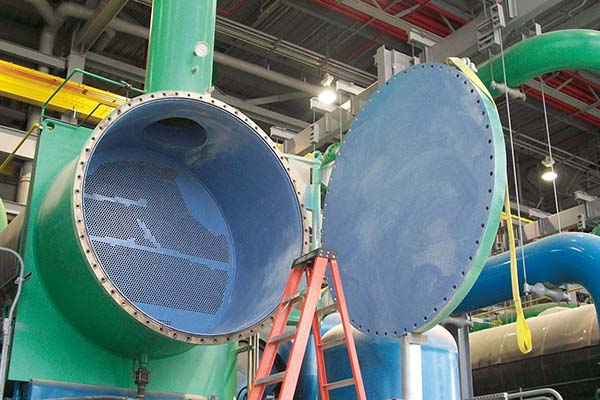
We can easily repair or recoat Belzona internal linings, so you don’t need to replace the entire lining should it be damaged. This simplifies maintenance and saves you money by further increasing service life.
Banks Industrial Group specializes in above-ground storage tank insulation, protective coatings, concrete, and related maintenance and repair services. Our innovative and cost-saving solutions help keep your facility running efficiently. For more information about our internal tank coating and vessel linings services and other industrial solutions, contact our team today by calling 856-687-2227.