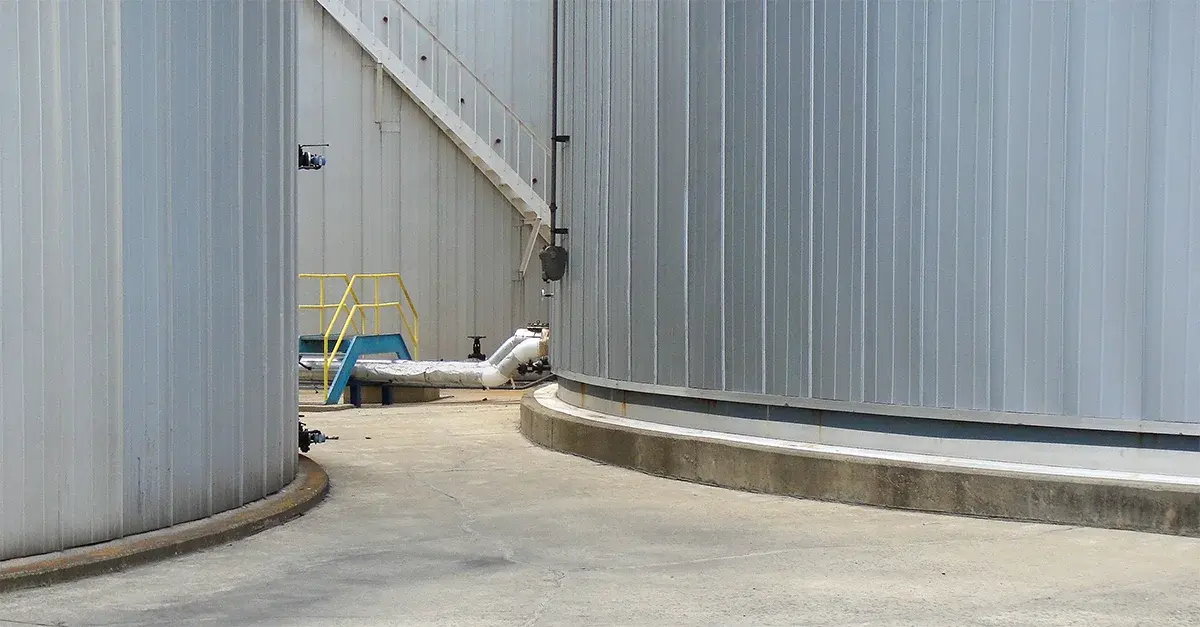
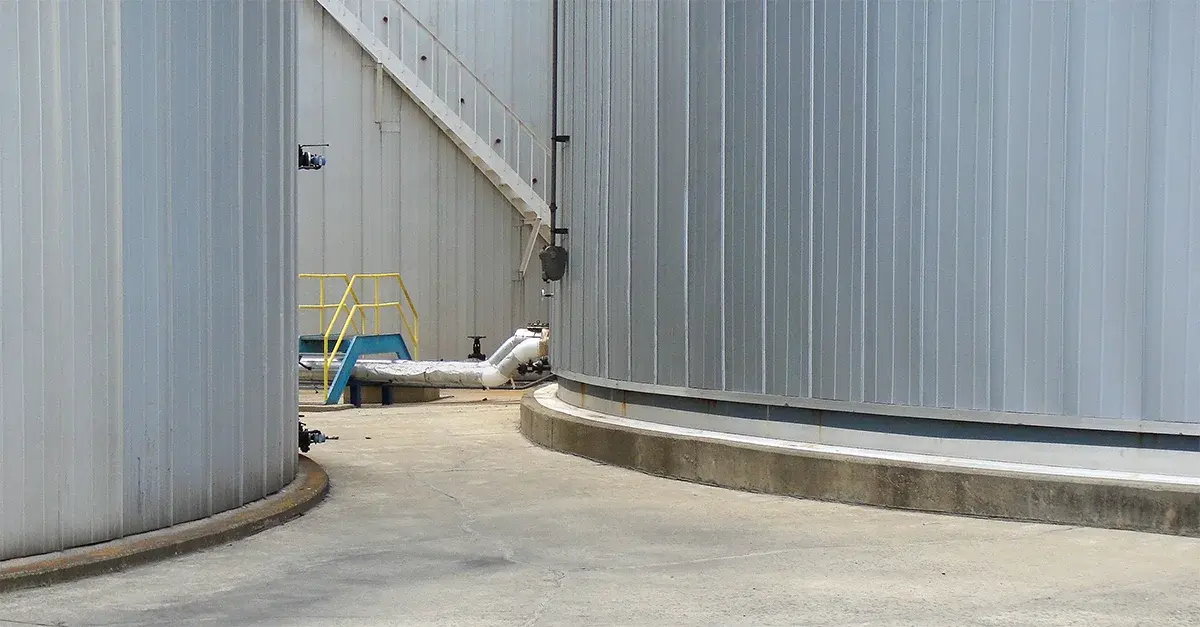
Storage tanks play a critical role in industries that store bulk liquids, such as oil and gas, chemical processing, and food production. These tanks, often insulated to maintain the temperature of their contents, require regular maintenance and inspection to ensure structural integrity. When it comes to insulated tanks, the inspections become more complex as the insulation conceals the tank’s surface, potentially hiding signs of corrosion or wear. To mitigate these risks, API 653 provides guidelines for inspecting and maintaining above ground storage tanks.
In this blog, we’ll explore the importance of regular inspections for insulated storage tanks, emphasizing the monthly, 5-year, and 10-year inspection requirements under API 653, while also discussing how inspection ports can assist in simplifying the inspection process without compromising on safety or tank performance.
API 653 is a standard developed by the American Petroleum Institute (API), designed to regulate the inspection, repair, alteration, and reconstruction of aboveground storage tanks (ASTs). These regulations are essential for ensuring the safe operation of tanks that store potentially hazardous or temperature-sensitive materials.
Regular inspections are crucial under API 653 to monitor tank conditions and detect any early signs of damage, particularly corrosion. Insulated tanks pose additional challenges since their insulation can mask underlying issues. The inspection intervals under API 653 are as follows:
Failure to adhere to these regular inspection intervals can lead to severe consequences, including tank failures that may result in hazardous spills, environmental damage, and costly repairs. One significant risk for insulated tanks is hidden corrosion—corrosion that forms beneath the insulation where it cannot be seen during routine inspections.
Our company has seen this happen in the past. A storage tank from one of our customers had just passed its 10-year inspection and began leaking after only three months of being returned to service. The corrosion, hidden beneath layers of insulation, had gone undetected during the inspection and led to a costly leak and operational disruption. This real-world example highlights the critical importance of adhering to inspection guidelines to ensure that even hidden damage is caught before it becomes a significant problem.
Insulation panels are removed from the lower tank wall and supported to expose the corrosion-prone tank chime angle, simplifying API 653 corrosion inspections.
Inspecting insulated storage tanks presents unique challenges, particularly when it comes to accessing hidden areas. Insulation not only prevents inspectors from performing a full visual examination, but it also creates an environment where moisture can accumulate, promoting corrosion. The insulation’s metal jacketing can trap water, further accelerating damage.
To overcome these challenges, tank owners can employ several best practices that make inspections more efficient and thorough, even for insulated tanks:
Insulation inspection ports simplify tank wall testing by providing access to the tank wall without removing the insulation.
To make inspections even easier and more consistent, many tank owners can install inspection ports. These ports are simple, cost-effective solutions that allow for easy access to the tank’s surface beneath the insulation, enabling inspectors to perform NDT measurements without removing large sections of insulation.
Inspection ports are particularly useful for tracking corrosion rates over time. By installing these ports at key locations, such as around the tank’s base or in areas known to experience higher rates of wear, inspectors can ensure that they are monitoring the same location during each inspection, allowing them to track the degradation of wall thickness accurately.
Installing inspection ports can also reduce the amount of labor required to inspect insulated tanks, as inspectors may no longer need to remove and replace large portions of insulation for each inspection. Instead, they can simply remove the plug from the port, perform their measurements, and reinstall the port to maintain the insulation’s integrity.
Regular inspections are essential for maintaining the long-term health and safety of insulated storage tanks. By adhering to API 653’s guidelines and utilizing inspection tools such as inspection ports, tank owners can detect early signs of corrosion and other damage, preventing costly repairs and downtime.
Proper maintenance practices also help ensure compliance with regulatory standards, which are not only designed to protect the environment but also to prevent accidents that can put human lives at risk. Tanks that are regularly inspected and maintained are less likely to experience sudden failures, reducing the risk of hazardous spills or catastrophic damage.
For storage tanks covered in insulation, maintaining compliance with API 653 requires a proactive approach to inspections and maintenance. By implementing regular inspection intervals—monthly, 5-year, and 10-year inspections—facility owners can stay ahead of corrosion and other risks. Incorporating inspection ports into the maintenance routine allows for more efficient inspections, providing easy access to the tank surface for NDT measurements while reducing labor costs and ensuring the tank’s long-term integrity.
With the right strategies in place, insulated tanks can be safely maintained, reducing the risk of costly failures and ensuring that the facility remains compliant with industry standards for years to come.