Overcoming Inspection Challenges for Insulated Storage Tanks
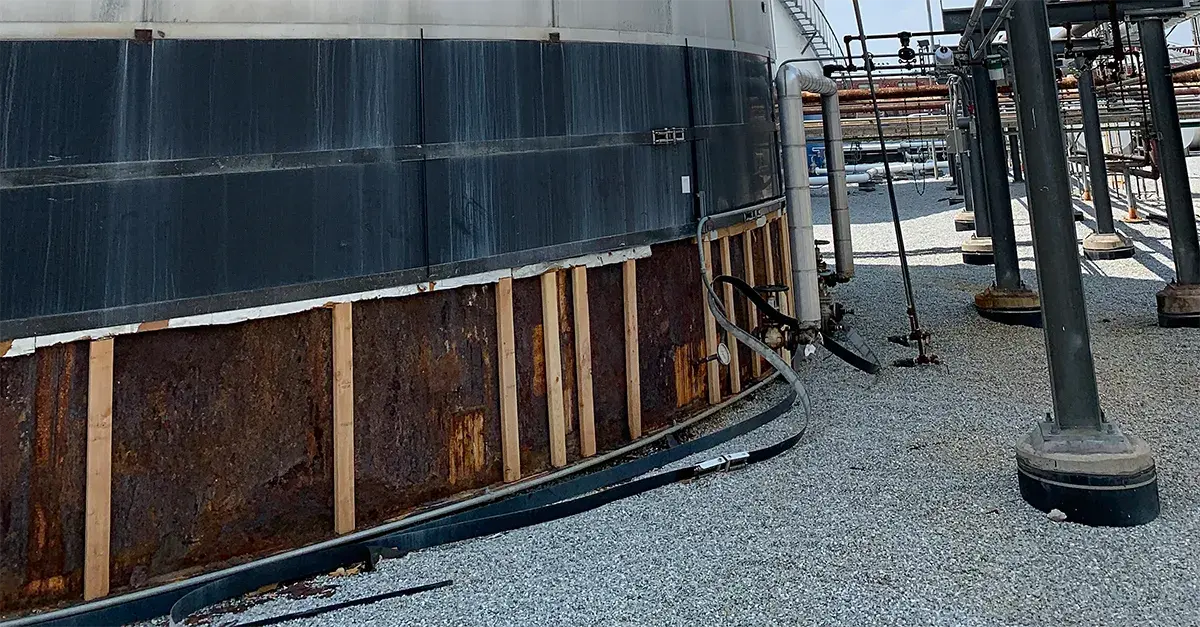
Contents
Insulated storage tanks play an essential role in industries like oil and gas, chemical processing, and food production. These tanks help maintain stable temperatures for materials, ensuring operational efficiency and safety. However, insulation, while necessary for temperature regulation, creates significant challenges when it comes to regular maintenance and inspection. Corrosion and damage can hide beneath the insulation, creating risks that are difficult to detect during routine checks.
This blog will explore the common challenges faced when inspecting insulated storage tanks and discuss how these challenges can be overcome. Additionally, we’ll touch on how inspection ports can be used to improve access during inspections, ensuring long-term compliance with API 653 and extending the lifespan of storage tanks.
The Challenges of Inspecting Insulated Storage Tanks
Insulating storage tanks helps protect contents from external environmental factors such as temperature fluctuations and exposure to the elements. While insulation serves its purpose of protecting the tank, it can also make regular inspection and maintenance more complex and costly. Here are some of the most common challenges encountered:
Corrosion hidden under insulation can be a huge problem.
1. Hidden Corrosion Beneath Insulation
One of the most significant challenges with insulated tanks is the potential for hidden corrosion. Insulation materials often trap moisture against the surface of the tank, particularly when the insulation or its protective metal jacketing becomes compromised. This trapped moisture can accelerate corrosion on the tank’s surface, especially in areas near weld seams, at the tank base, or where the insulation is poorly sealed.
Because the corrosion occurs beneath the insulation, it can go unnoticed during routine visual inspections. Corrosion can weaken the tank walls over time, potentially leading to leaks, tank failures, or other costly problems. Without regular and thorough inspection of these insulated areas, tank owners run the risk of missing critical signs of corrosion.
Corroded tank chime angle is revealed beneath insulation panels.
2. Difficulty in Accessing Critical Areas
Insulation systems often cover key areas of the storage tank that are vulnerable to damage, such as the tank base and corner welds where the tank shell meets the floor. These areas are prone to corrosion due to moisture accumulation, especially when the insulation traps water at the base of the tank. However, the insulation makes it difficult for inspectors to properly assess these areas during regular checks.
Without easy access to these critical regions, inspectors may not be able to detect early signs of degradation or corrosion that could jeopardize the tank’s structural integrity. Removing large sections of insulation for every inspection is not always feasible, as it can be costly and time-consuming, often requiring specialized labor to restore the insulation afterward.
Dented and corroded tank insulation allows water infiltration from tank roof.
3. Challenges with Metal Jacketing and Insulation Integrity
Many insulated storage tanks are covered with metal jacketing that helps protect the insulation from environmental wear. Over time, the jacketing can degrade or suffer from mechanical damage, such as dents, cracks, or corrosion, which can allow water to penetrate the insulation and become trapped between the jacketing and the tank surface.
Once water has infiltrated the insulation, it accelerates the corrosion process on the tank wall. Because this corrosion happens underneath the jacketing, it often remains hidden until it causes significant damage. Inspectors may not be able to identify this issue unless the jacketing is removed, adding more complexity to the inspection process.
Insulation removed for work access must be replaced.
4. Cost of Comprehensive Inspections
Due to the difficulties of inspecting insulated storage tanks, conducting thorough inspections often requires removing and replacing large sections of insulation. This can be expensive and time-consuming, especially for large tanks. For tanks that store critical materials and cannot easily be taken out of service, the cost of downtime can add to the overall expense of the inspection process.
Given these challenges, it is essential to find ways to conduct regular inspections that are both cost-effective and thorough, without compromising the tank’s insulation or structural integrity.
Best Practices for Overcoming Inspection Challenges
Despite these obstacles, there are several best practices that can be implemented to make the inspection process more efficient and effective, even for insulated storage tanks. These practices help ensure that tanks remain in compliance with API 653 standards and reduce the risk of hidden corrosion leading to costly failures.
Insulation removed from tank chime angle facilitates API 653 inspections.
1. Exposing Critical Weld Areas for Inspection
A common best practice for insulated storage tanks is to expose critical weld areas, such as the corner welds at the base of the tank, for regular visual inspection. This can be done by raising the insulation slightly at the tank base, allowing inspectors to view the most vulnerable parts of the tank without removing large portions of insulation. By keeping these areas visible, inspectors can monitor them for signs of moisture or corrosion more regularly.
This method is particularly important for API 653 compliance, as it allows tank owners to focus on inspecting high-risk areas that are prone to corrosion. Exposing critical welds helps ensure that potential issues are caught early, reducing the risk of leaks or tank failures caused by hidden damage.
2. Implementing Non-Destructive Testing (NDT)
Non-destructive testing (NDT) techniques, such as ultrasonic thickness testing, are invaluable for monitoring the condition of insulated tanks without the need to remove insulation. NDT allows inspectors to measure wall thickness and detect corrosion beneath the insulation, providing a more accurate assessment of the tank’s overall health.
By performing NDT regularly, tank owners can identify areas of concern early and schedule maintenance before the damage becomes severe. This proactive approach helps prevent costly repairs and ensures that tanks remain in compliance with API 653.
Insulation inspection ports enable NDT testing without removing insulation panels.
3. Using Inspection Ports to Simplify Inspections
One of the most effective ways to overcome the challenges of inspecting insulated storage tanks is to install inspection ports. These ports provide direct access to the tank surface beneath the insulation, allowing inspectors to perform non-destructive testing without removing large sections of insulation.
Inspection ports are easy to install and cost-effective, making them a valuable tool for long-term tank maintenance. By strategically placing inspection ports in areas known to experience high wear, such as around weld seams or moisture-prone areas, tank owners can ensure that these critical areas are regularly inspected.
Additionally, inspection ports make it easier to track the degradation of wall thickness over time, as inspectors can measure the same location during each inspection. This consistency helps tank owners monitor corrosion rates more accurately and plan maintenance accordingly.
Storage tank insulation damaged during wind storm.
4. Regularly Checking Metal Jacketing and Insulation Integrity
It’s important to regularly check the condition of the metal jacketing and the insulation itself for signs of damage or wear. Any cracks, dents, or openings in the jacketing should be repaired promptly to prevent moisture from penetrating the insulation. By addressing these issues early, tank owners can reduce the risk of hidden corrosion and prolong the lifespan of both the insulation and the tank.
Visual inspection of caulking utilized to seal joints is an important part of the tank inspection process. Some areas to look for might include the following:
Stair steps welded to the tank allow for many joints or seams that need to be caulked for prevention of water intrusion. Each step will have a seam where the insulation needed to be cut around the step during installation. Modern tank practices incorporate stringer stairs that eliminate the need to weld each step to the tank shell.
A joint for water intrusion may be located where the tank shell insulation meets the tank roof. This area is a critical seal as water running off the roof could be draining down behind the tank shell insulation.
All the vents or handrails at the tank roof need to be caulk sealed to prevent water infiltration.
Manways and piping leading into and out of the tank may be an area of water intrusion.
Remember, caulking doesn’t last forever. This is one of the cheapest repairs owners can make to help maintain this very expensive asset.
Conclusion
Inspecting insulated storage tanks presents unique challenges, particularly when it comes to detecting hidden corrosion and accessing critical areas. However, by implementing best practices such as exposing weld areas, using non-destructive testing techniques, and installing inspection ports, tank owners can overcome these challenges and ensure that their tanks remain compliant with API 653 standards.
Inspection ports are especially valuable for simplifying the inspection process, providing direct access to high-risk areas without the need for costly insulation removal. By incorporating these tools and techniques into regular maintenance routines, tank owners can detect corrosion early, reduce the risk of tank failure, and extend the lifespan of their storage tanks.
Proactive inspections are essential for maintaining the long-term health and safety of insulated storage tanks. With the right strategies in place, tank owners can ensure that their tanks continue to operate efficiently and safely for years to come.