Insulated Tank Maintenance Best Practices For Long-Term API 653 Compliance
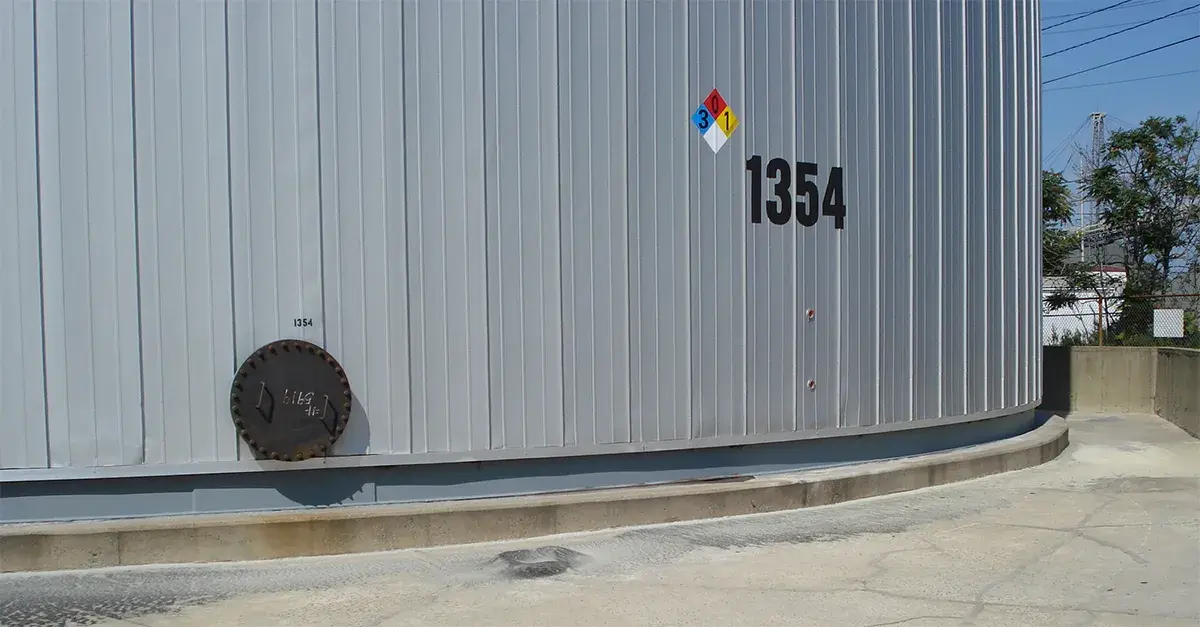
Contents
Insulated storage tanks are critical assets in industries such as oil and gas, chemical processing, and food production. These tanks store temperature-sensitive or hazardous materials that must be kept at specific conditions to ensure safe and efficient operations. However, maintaining insulated tanks presents a unique set of challenges, particularly when it comes to complying with API 653 standards, which govern the inspection, repair, alteration, and reconstruction of aboveground storage tanks (ASTs).
Insulation, while crucial for temperature regulation, can obscure signs of damage, such as corrosion or structural wear, making regular maintenance more difficult. In this blog, we will explore best practices for maintaining insulated storage tanks to ensure long-term compliance with API 653. We’ll also discuss how tools like inspection ports and insulation support systems can simplify the maintenance process without compromising tank integrity.
The Importance of API 653 Compliance for Insulated Tanks
The American Petroleum Institute (API) developed API 653 as a standard to regulate the safe operation and maintenance of aboveground storage tanks. These standards are essential for preventing tank failures, ensuring environmental safety, and maintaining operational efficiency.
For insulated tanks, API 653 compliance becomes more complex because insulation can conceal potential problems such as corrosion or thinning of the tank wall. Inspections, repairs, and alterations are more difficult to perform on insulated tanks because the insulation itself can hide signs of damage that would otherwise be easily detected.
Adhering to API 653 guidelines means ensuring that tanks are regularly inspected both externally and internally to detect early signs of wear or damage. For insulated tanks, this requires a proactive approach that incorporates the latest techniques for inspecting, maintaining, and repairing tanks covered in insulation.
Best Practices for Insulated Tank Maintenance
To ensure long-term API 653 compliance, tank owners must adopt best practices that allow for thorough inspection and maintenance without compromising the effectiveness of the insulation. Below are some of the most effective strategies for maintaining insulated storage tanks.
Tank base weld seam is exposed for easy inspection.
1. Expose Critical Weld Areas for Regular Inspection
One of the most vulnerable areas of any storage tank is the corner weld, where the tank shell meets the floor, also known as the chime area. This weld is particularly prone to corrosion because moisture often accumulates at the tank base, especially if the insulation traps water against the surface. Left unchecked, corrosion in this area can lead to significant structural damage and potential tank failure.
A best practice for maintaining insulated tanks is to raise the insulation slightly at the base of the tank to expose this critical weld area. This allows for regular visual inspection of the most vulnerable part of the tank, ensuring that moisture buildup or early signs of corrosion are detected and addressed before they become major problems.
Exposing the tank base also aligns with API 653 inspection standards, which emphasize the importance of inspecting key areas that are most susceptible to damage. By making these areas accessible, tank owners can ensure that they are staying ahead of potential risks.
Tank insulation panels are lifted slightly to expose the tank base.
2. Use Insulation Support Systems to Enhance Maintenance Accessibility
For tanks that are insulated, it is essential to have a system in place that allows for regular inspections and repairs without having to remove large sections of insulation. This is where insulation support systems come into play. These systems are designed to hold insulation off the surface of the tank, particularly at critical areas such as the tank base, corner welds, and other high-risk areas.
By using insulation support systems, tank owners can keep the insulation intact while still allowing inspectors and maintenance teams to access key areas for visual inspections or non-destructive testing (NDT). These systems not only help protect the tank from corrosion but also reduce the amount of labor required to remove and replace insulation during inspections.
Some insulation support systems are designed to be installed without the need for welding or extensive hot work, making them ideal for tanks that need to remain in service during maintenance. This minimizes downtime and reduces the cost of inspections and repairs.
3. Implement Regular Non-Destructive Testing (NDT)
In addition to visual inspections, non-destructive testing (NDT) methods are essential for monitoring the condition of insulated storage tanks. NDT techniques, such as ultrasonic thickness testing, allow inspectors to measure the wall thickness of the tank without having to remove the insulation. This is particularly useful for detecting hidden corrosion that may be developing beneath the insulation layers.
NDT should be performed regularly, in line with API 653’s recommended inspection intervals. By conducting these tests at key areas of the tank, particularly at weld seams and the tank base, tank owners can track the degradation of the tank’s wall thickness over time and address any areas of concern before they lead to more significant damage.
Insulation inspection ports facilitate tank wall corrosion testing.
4. Install Inspection Ports for Easy Access
One of the most effective tools for simplifying the inspection process on insulated tanks is the installation of inspection ports. These ports provide a quick and easy way to access the tank surface beneath the insulation, allowing for regular NDT measurements and visual inspections without the need to remove large sections of insulation.
Inspection ports are particularly useful for monitoring areas prone to corrosion, such as the tank base and corner welds. By installing these ports at strategic locations, inspectors can measure wall thickness and check for signs of corrosion over time. The ports are designed to be easily sealed after each inspection, maintaining the integrity of the insulation while still allowing for easy access during future inspections.
Additionally, inspection ports can reduce the overall cost of inspections by minimizing the amount of labor required to remove and replace insulation. This allows for more frequent inspections, ensuring that potential issues are caught early and addressed before they lead to costly repairs or tank failures.
Poor drainage contributes to tank base corrosion.
5. Ensure Proper Drainage Around the Tank Base
Another key aspect of maintaining insulated tanks is ensuring that there is proper drainage around the tank base to prevent moisture from accumulating. Moisture buildup at the base of the tank is one of the leading causes of hidden corrosion, especially in insulated tanks where the insulation can trap water against the tank surface.
To prevent this, tank owners should regularly inspect the area around the tank base for signs of moisture or standing water. In some cases, installing drainage systems or sloping the ground around the tank can help divert water away from the base, reducing the risk of corrosion.
Ensuring proper drainage is particularly important for complying with API 653, as it helps reduce the risk of corrosion at the most vulnerable part of the tank.
Long-Term Benefits of Proactive Maintenance
By following these best practices for insulated tank maintenance, tank owners can significantly reduce the risk of tank failure and extend the lifespan of their storage tanks. Regular inspections, combined with the use of insulation support systems and inspection ports, allow for a more thorough understanding of the tank’s condition, enabling owners to make informed decisions about repairs and maintenance.
Proactive maintenance also ensures compliance with API 653, which is essential for avoiding regulatory fines and minimizing environmental risks associated with tank failures. By investing in proper maintenance, tank owners can protect their assets, reduce downtime, and ensure the safe and efficient operation of their storage systems.
Conclusion
Maintaining insulated storage tanks requires a proactive and comprehensive approach to inspection and repair. By exposing critical weld areas, using insulation support systems, performing regular non-destructive testing, and installing inspection ports, tank owners can ensure that their tanks remain compliant with API 653 standards while reducing the risk of costly failures.
Proper maintenance practices not only help extend the life of the tank but also ensure that the tank operates safely and efficiently for years to come. With the right strategies in place, insulated tanks can be inspected and maintained without compromising their insulation, ensuring long-term compliance and reliability.