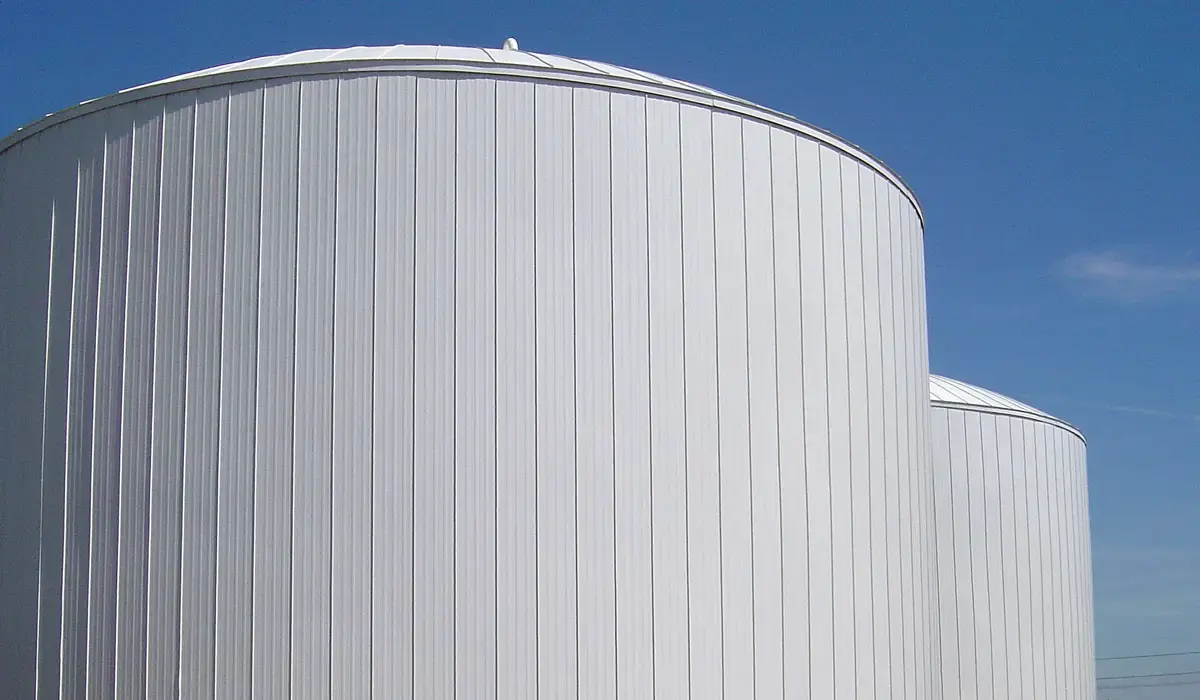
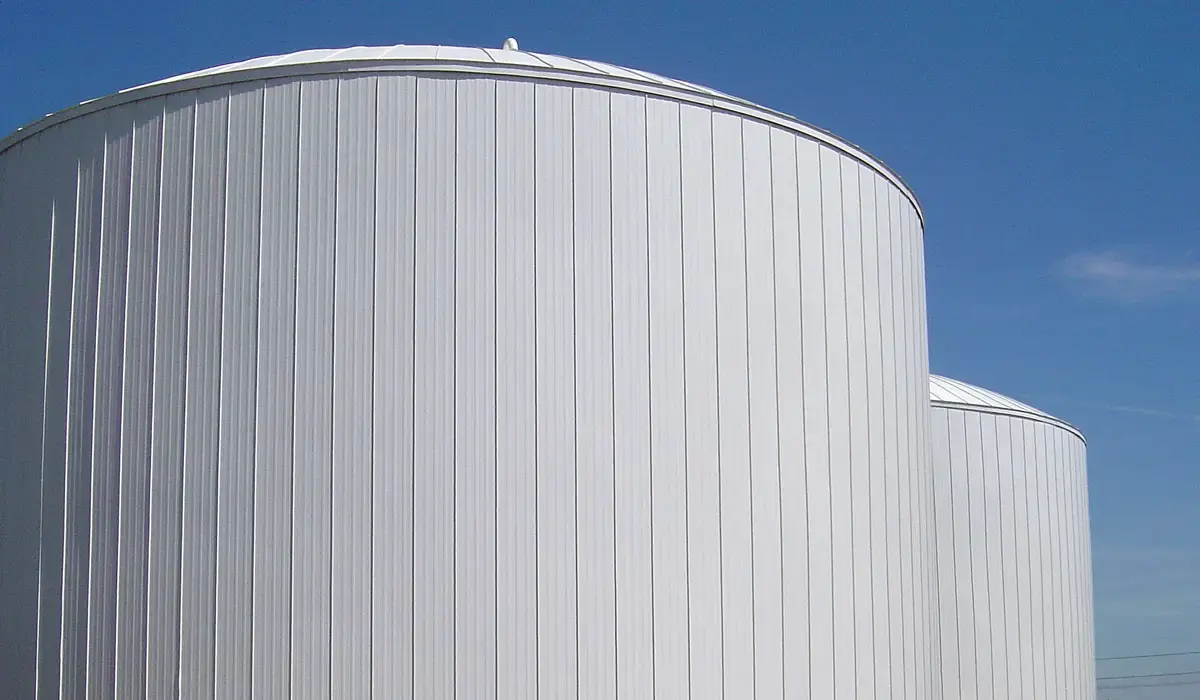
Most plant managers looking to insulate a bulk storage tank will predictably want to know the cost before doing it. Although the average cost to insulate a storage tank is approximately $10 per square foot, many factors will alter the development of that price.
Here are the top 9 questions you need to ask when insulating a storage tank to determine the total cost of the job:
When insulating a tank, the first thing you need to know is the size – the circumference, the diameter and the height. These parameters determine the required surface area. Our vertical insulation panels are 24 inches wide, and the length is customized to fit the full height of your tank.
The shape of the roof (flat, cone or dome) will determine the technical approach to insulating it. For standing seam roofs, radial, X, straight and tapered designs are available with the option for non-welded roof plate attachments. If you are insulating the roof, the ability to weld down the attachment system is a major factor in determining the cost of installation. Be sure you consult with your vendor early in the process to determine the most direct and cost effective method of installing the roof attachment system.
When no existing insulation is on the storage tank, a crew can begin the insulation process almost immediately. Stripping off existing insulation will add cost to a full replacement along with addressing issues that may arise when the tank shell is exposed. Stripping the existing insulation may reveal corrosion under insulation (CUI), a problem which will require attention.
Accessing the roof of the tank with either stairs or ladders installed on the tank can require custom cutouts in the insulation. Generally speaking, stairs will add more cost than ladders because of an increased number of cutouts especially when the stairs are welded directly to the tank. Utilizing stringer staircase methods will reduce the number of cutouts and therefore the cost. Ladders are typically the easiest to insulate around and therefore lower in cost.
Barriers such as dike walls reduce the accessibility of the job site, requiring more time to enable deliveries of material, tools and labor. In some cases, access points may need to be built to enable these deliveries or special lifting apparatus such as cranes will need to be employed.
The product in the tank will determine the insulation specifications. Products like asphalt must be kept at an operating temperature between 280 to 350 degrees Fahrenheit, in turn adding multilayer insulation requirements for the shell. For lower temperature products like biodiesel (~90 degrees Fahrenheit) requirements for the tank can be accomplished through a single layer of insulation. Products stored above 230 degrees Fahrenheit need special care in selection of materials.
The presence of corrosive products will also drive insulation costs. A corrosive product, such as caustic soda, will dissolve aluminum so this must be considered when selecting the protective metal outer skin. Installing stainless steel or coated Galvalume steel can drive up the cost of the project because of material costs or additional labor to install. Inspection ports can be installed on tanks to check the condition of the tank wall and wall thickness without removing the insulation.
The location of the installation, associated shipping charges from the manufacturer of the insulation materials, as well as the prevailing wage and/or union labor rates can drive the cost of an installation. Out of town installation crews requiring per diem or travel costs also factor into the cost. Installations in cold or rainy climates (especially in winter months) will add to the length of installation time and thus drive labor costs. Windy conditions can unfortunately affect price because safely controlling long insulation panels is a bit like controlling kites. Sustained winds over 15 knots can easily shut down a job site due to unsafe working conditions.
Poorly insulated tanks reduce efficiency, add energy costs, accelerate equipment failures and condensation and increase safety risk within an industrial facility. Failure to maintain stored materials at the adequate temperature range can prevent them from being pumped or moved. The right insulation materials installed by professionals can eliminate or mitigate all of these factors. The process is not hard or complicated, but requires close attention to the details and management of expectations.
To request a storage tank insulation estimate online, use our online estimate form.
Need to know more? Schedule a lunch and learn - we'll provide sustenance and learning for your team. For more assistance, email or call us at 856-687-2227 for recommendations, estimates and schedules.