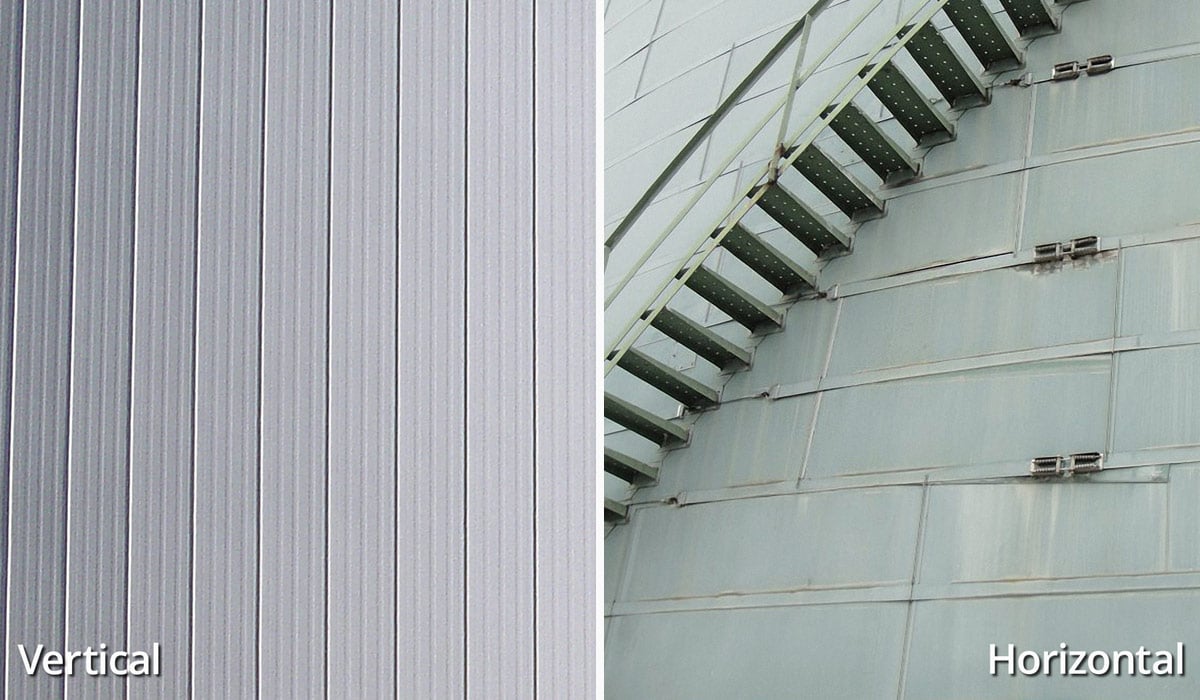
Contents
Large bulk storage tanks require insulation to store heated products. The asset owner can choose from the following types of insulation to meet the storage tank insulation requirement:
- Vertical panel system
- Horizontal panel system
- Spray on foam
- Conventional or screwed on system
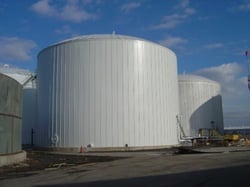
Since most clients today typically select vertical or horizontal panel type insulation systems, this blog will discuss the positive and negative aspects of both systems. Both systems manage energy costs and protect tanks with varying degrees of success. Most engineers want to know: which is better?
The panels names explain the basic difference. Vertical panels install vertically to the bulk storage tank utilizing an internal cable system. Conversely, horizontal panels stack in rings around the tank from the base to the roof, secured in place by external bands.
Let’s take a look at the similarities and differences, then dive into the benefits of each.
What are the similarities between vertical and horizontal insulation panels?
1. Metal thickness: Both insulation panel types will typically use a .024 thick aluminum as the outer shell material.
2. Insulation type: Both panel systems use the same type of insulation, typically polyisocyanurate foam insulation (for tanks up to a 250-degree maximum threshold) and polyisocyanurate foam combined with fiberglass for tank storage requiring higher temperatures.
3. Expansion and contraction: Both types of panels allow for expansion and contraction of the insulation system as temperature varies, albeit via different methods. The standing seams on vertical panels allow for natural expansion or contraction. Horizontal panels utilize springs incorporated within the external bands to achieve the same objective.
What are the differences between vertical insulation panels and horizontal insulation panels?
1. Panel size: Vertical panels measure two feet wide and can be manufactured in one or two pieces to the height of the tank. Single-piece panels are limited to 50 feet (the maximum length of a shipping trailer). Horizontal panels measure four feet by eight feet. Installers then stack each panel on top of another with an offset of the seams.
2. Connections: Vertical panels attach to an internal cable system installed in three foot increments up the side of the tank. Technicians then loop a stainless-steel strap around the internal cable and incorporate the strap into the standing seam of the insulation panel. This method draws the panel into the tank tightly but still allows for expansion and contraction. By contrast, horizontal panels stack adjacent to each other until they reach the top of the tank. External bands with spring loaded tension clips hold them in place.
3. Seams: Vertical panels use a double fold standing seam to mate one panel to the next. The double fold standing seam resembles the rim around the top of a soda can and creates a watertight seal. Additionally, the vertical standing seam from panel to panel allows for system expansion and contraction during temperature swings. On the other hand, horizontal panels come with overlapping seams between each panel that create a watershed effect as moisture descends down the side of the tank from the roof.
4. Tank door access: To accommodate entrance into a tank during a turnaround, a framework or clips need to be weld installed for either system. The vertical panels must be cut to expose the internal cables attached to the new framework or clips. This approach requires new panels to be manufactured for installation in the door sheet, a downside. However, utilizing a door sheet framework allows the area to be opened up again for tank access during the next turnaround. The horizontal system requires a similar door access system where the external bands attach to the framework or clips. The horizontal panels can be removed in order to achieve the same result, and those panels can be reused once the turnaround is complete.
Are vertical insulation panels better than horizontal insulation panels?
Both panels can reasonably meet a customer’s needs for insulation. However, vertical panels exhibit some traits that can reduce risk for those who choose them. Let’s look at each advantage.
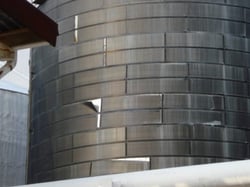
1. Reliability. Delamination can cause problems for horizontal panels, as the panels tend to shift when the foam insulation delaminates from the aluminum shell. These shifts can leave gaps in the external insulation shell, providing an opening for moisture intrusion. High winds can exacerbate these gaps, causing further damage to a horizontal system. Delamination can also occur in vertical systems but without practical impact since the panels attach in 3 foot increments to the internal cables.
2. Ease of installation. Installation methods for horizontal panels typically require scaffolding, a hydraulic lift with a very large basket (enough to hold 2 workers along with 8 foot panels) or an elaborate hanging scaffolding. Vertical panels can be installed with a hydraulic lift or a painter’s basket hung from the roof of the tank. As horizontal panels stack up the tank during installation, they become susceptible to damage in the transition from installation to the finished product. Installers can protect vertical panels during the installation, reducing material cost risk to the customer. In general, installation of vertical panels tends to be easier, more resistant to weather during installation and creates cost-efficiencies for the owner.
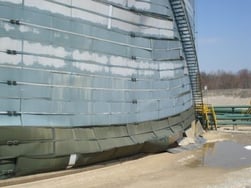
3. Total ownership costs. Vertical panels will reduce maintenance costs for the owner when compared to horizontal panels. First, horizontal panels require occasional monitoring and tightening of the bands which secure the panels to the tank. Failure to do so can lead to buckling of the horizontal system as shown below. Second, the potential for horizontal panels to slip down or shift create opportunities for moisture intrusion. This adds risk for corrosion under insulation damage and increasing heat loss on wet insulation. Moisture intrusion into a horizontal system increases the chance for complete system failure. The weight of the soaked insulation stresses the bottom rows, increasing the chance of buckling and complete failure.
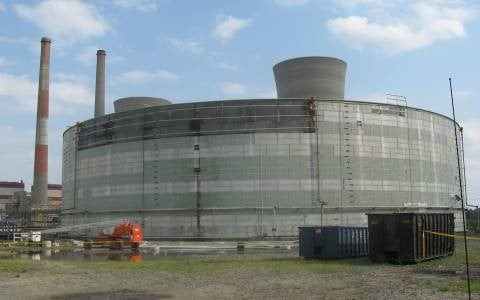
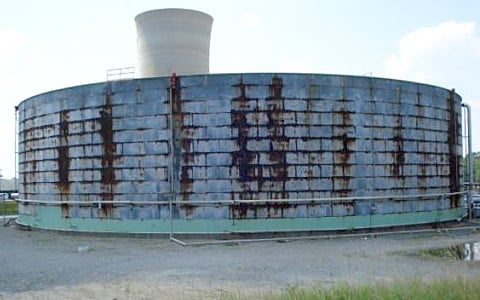
How can the disadvantages impact your storage tank insulation solution?
The two pictures below demonstrate the risk of moisture intrusion. They show the “before” of a horizontal system and the results following the stripping of the insulation. This insulation failure revealed significant corrosion under insulation, causing a major outage and expense for the asset owner to repair.
In short, before you select either system, plan your project with a professional storage tank insulation team who will take you through the design and cost considerations. Proactive planning will enable you to meet your insulation needs with the fewest changes and the greatest budget certainty.
Interested in learning more about the technical requirements of planning a bulk storage tank insulation project? Schedule a lunch and learn with our team today. We will provide lunch and information on solutions for your storage tank insulation needs.
Email or call us at 856-687-2227 now for assistance!
How to learn more about preventing corrosion on your bulk storage tank
Schedule a lunch and learn with our technical consultants. Find out how you can reduce your risk from corrosion and lower your total ownership costs.
Email or call us at 856-687-2227 now for assistance!