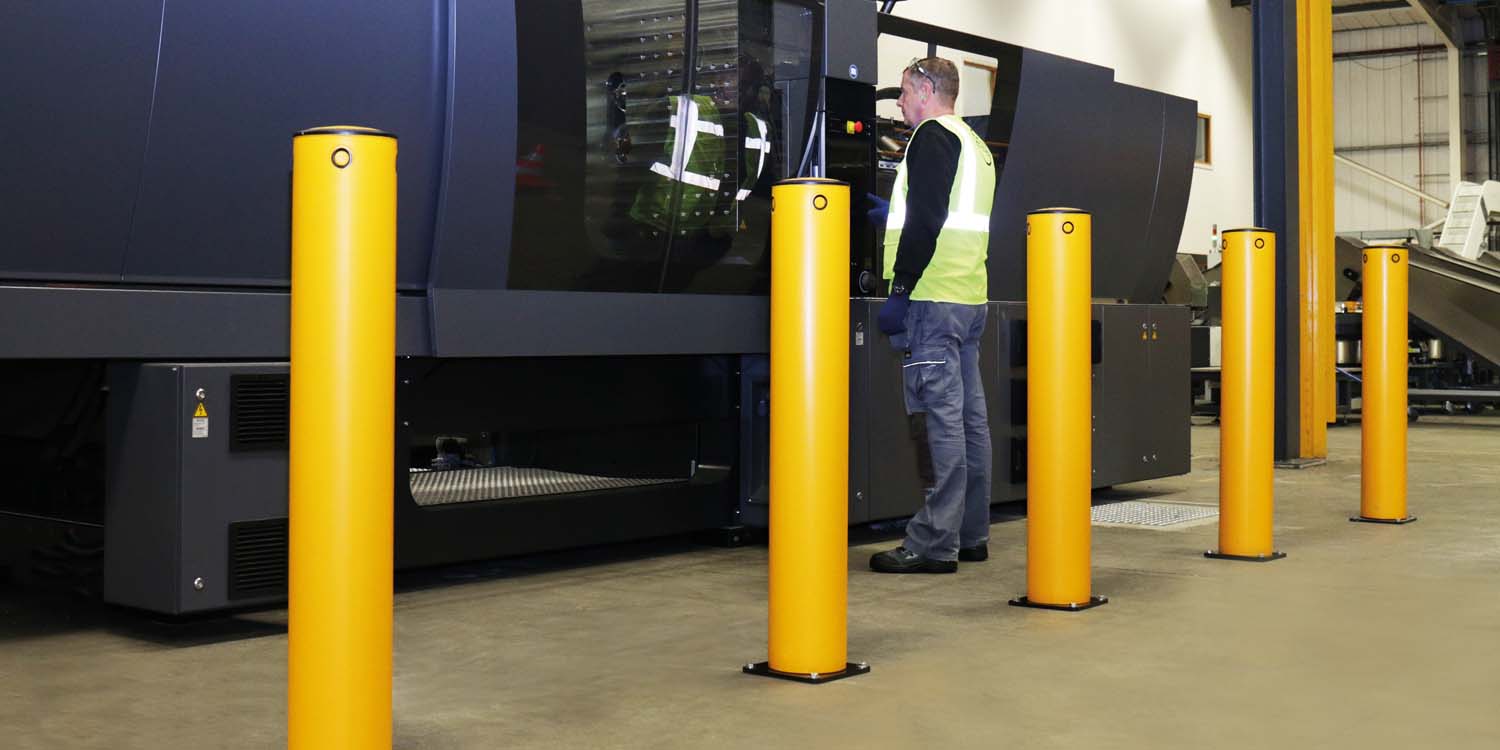
Contents
What began centuries ago as a simple post to moor a boat is today one of the most common safety features you’ll find almost any time you walk into an industrial space. Bollards act as common sentries on just about every loading dock and high traffic area inside a manufacturing plant, warehouse, or industrial facility. You will also find them more commonly in everyday commercial facilities like gas stations or any business with a drive-through accommodation. Since 9/11 changed security requirements around the world, bollards have multiplied and proliferated in buildings of all shapes and sizes everywhere. Their numbers reflect their impressive resume of risk mitigation and protection across a myriad of markets and applications.
First, here’s a little bollard trivia with which you can dazzle your facility manager.
The concept of tying something to a post to secure it is as old as time, but bollards (at least the word bollard) first came about in the 1700s when ships were tied to a “bole,” or trunk, of a tree. But it didn’t take long for people to discover other uses for them. As early as 1721, people used bollards for traffic guidance when two wooden posts were installed at a monument in Hertfordshire, England, to secure it “from injury by carriages” - and bollards have been on the job ever since.
Bollards can protect several aspects of your operation; people, machines, and even your building itself. They can also help manage traffic flow (for both cars and vehicles), and be a visual guide to easily identify an access point.
The Top 4 Most Common Uses of Bollards
- Security: Whether it’s a long row to keep forklifts and other traffic from veering into pedestrian spaces, or a defensive line in front of sensitive operational areas, bollards not only provide visual identification that an area is off limits, but stand as a physical deterrent against a variety threats, accidental and intentional.
- Protection of vulnerable machinery: A forklift-damaged piece of machinery on your production floor could cause downtime and loss of revenue. A truck-compromised gas meter or electrical panel on your building could be a very real danger to nearby people. A strategically placed bollard provides one of the easiest and cost-effective ways to keep your equipment safe.
- Damage prevention: A production facility can be a hectic environment, and even if a piece of machinery isn’t necessarily vulnerable, you don’t want it or other vehicles smashing into any operational asset, the surrounding infrastructure, or – most importantly—workers and visitors. Bollards can keep your business humming along safely, saving you money on downtime and vehicle/building repairs.
- Vehicle and pedestrian guidance: High visibility bollards in high-and-mixed-traffic locations help avoid those aforementioned collisions. Bollards that clearly mark where people and vehicles should travel will keep everyone moving in the right direction.
If you’re reading this blog, it’s a pretty safe bet that you are in “our world” of manufacturing, warehousing, or other industrial settings. However, bollards pop up everywhere in our daily lives.
- Airports: Security drives the need for bollards at any airport entrance. Tarmacs buzzing with ground support equipment, fueling or luggage vehicles can also benefit from the added protection.
- Gas Stations: Most people carefully pull up to the pump when it’s time to refuel, but one wayward driver can cause a catastrophe. Gas pump bollards are crucial to dispensing fuel safely.
- Parking Garages: Garages see hundreds of cars driving in and out on a daily basis. It is vital to protect load-bearing walls and columns, keep ticket machines and gate arms safe and to mark walking lanes and stairwell entrances.
- Commercial Locations: Bollards keep the outside perimeter of a store secure, and provide a number of uses in a retail setting. They keep customers from crashing a cart into a freezer, a floor cleaner from sweeping debris into an air intake, or a crowd of people from entering an escalator unsafely.
- Schools: There’s no line like an elementary school pickup line. When parent vehicles start filing in to pick up their little ones, well-placed bollards separate traffic and keep children free from danger.
- Loading docks: Accidents around loading docks tend to be expensive. Trucks backing into buildings, corner collisions with forklifts and separating machines and humans can all be avoided with a simple bollard.
- Playgrounds: Today’s playgrounds are safer than ever thanks to plastic equipment and rubber mulch covered ground, but bollards take that safety to another level. Urban settings leave little room between a playground and roads. Bollards protect equipment that can cost hundreds of thousands of dollars and keep children separate from vehicular harm.
In short, while bollards shine in locations of potential impact or accident, they provide benefit where humans and machines interact. They keep important things safe while still providing access, and provide a strong visual alert to drivers.
That’s the how, why, and where bollards are most often used, but let’s touch on the “what” for a moment…what materials are used most for bollards? Steel (iron alloy and stainless), aluminum, cast iron, concrete, plastic, and polyurethane are the materials most frequently used to make bollards. Of that list, steel and polyurethane (polymer) are the ones most often found in the industrial settings. Discussing the differences, benefits, and considerations of these two types of bollards merits its own blog…in fact, we’ve already written it! It’s a quick read that we highly recommend, but here are the highlights.
Steel vs Polymer
- Availability is the best ability: The MOST important element of bollards is that you HAVE them. Yes, there are many differences and considerations between steel and polymer to dissect, but ultimately, doing SOMETHING to protect equipment, goods, infrastructure, and people is paramount.
- Total cost of ownership: When considering which material bollard to use, think about durability and maintenance costs over the years you will need it in service. Polymer barriers, unlike denting steel, absorb impacts and retain their shape. They also do not require the periodic repainting and upkeep that steel barriers do. The damage transfer from barrier to vehicle is also less with polymer, making fleet repairs and replacement notably less with polymer. While both are effective in the moment at providing a safety barrier against accidents and injuries.
The BIG Takeaway
- Bollards are ubiquitous in almost any retail or manufacturing setting.
- They’re one of the easiest and most cost-effective measures of providing multi-faceted protection.
- Bollards can absorb up to 80% of an impact, keeping your machinery, structures, products, employees, and customers safe.
Our BIG Solution
If safety is a priority for your company, Banks Industrial Group can protect your people and your property with bolt-down, flexible bollards that are scientifically engineered and tested for safety. Banks Industrial Group can provide both sales and installation of A-SAFE iFlex bolt down bollards, as well as train your staff to install them. For more information, please contact us.